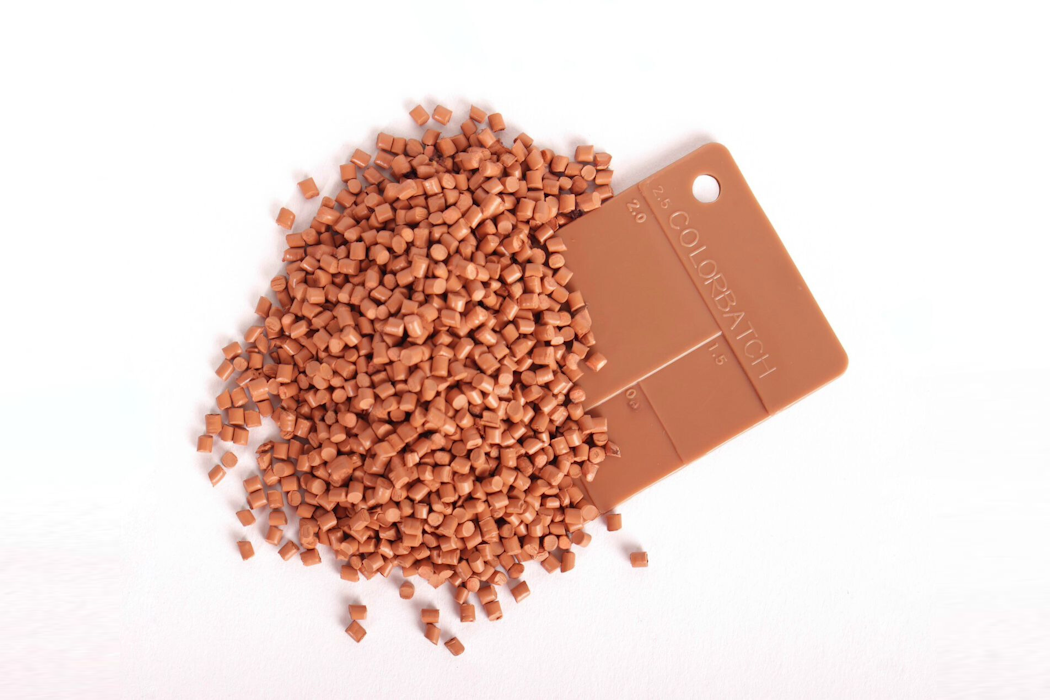
Siete claves para un desarrollo de color eficiente en envases plásticos
En envases, recipientes y contenedores plásticos para el hogar — como organizadores, cajas, botes, portarretratos o maceteros — cada proceso de fabricación presenta retos específicos. La extrusión (convencional, soplado o coextrusión) requiere alta dispersión del masterbatch para evitar ráfagas, además de resistencia térmica, estabilidad al exterior y compatibilidad en multicapa. La inyección (convencional o soplado) demanda compatibilidad pigmento-resina, resistencia a presión y temperatura, buena dispersión y precisión en el tono, especialmente en piezas delgadas. El termoformado exige formulaciones que mantengan el color uniforme pese a variaciones de espesor tras el conformado.
Para alcanzar resultados óptimos, es fundamental considerar el sistema de pigmentación, el tipo de resina, opacidad o transparencia, estabilidad térmica del pigmento, el proceso y tiempo de residencia, así como el espesor del producto final. Además de evaluar el tipo de equipo dosificador (manual, volumétrico o gravimétrico).
Masterbatch vs. Pigmento en Polvo: ¿Cómo elegir?
Ambas opciones tienen ventajas, pero la elección debe basarse en el proceso, el nivel de control y el costo total de pigmentación. Este costo no solo incluye el precio por kilo, sino también la concentración del pigmento en el masterbatch, el porcentaje de aplicación, la eficiencia en la dispersión y costos indirectos como manejo, dosificación, limpieza, mermas, retrabajos, seguridad y control de calidad.
- Masterbatch: concentrado de pigmento en resina base que asegura mejor dispersión, manejo y repetibilidad. Se aplica en porcentajes del 1% al 5%, facilitando la dosificación automática y reduciendo tiempos de limpieza y rechazos. Requiere menos equipo especial de seguridad.
- Pigmento en polvo: usándose en porcentajes menores (0.5% a 2%), propenso a errores en la pesada crítica y dosificación. Su volatilidad puede causar contaminación cruzada y riesgos a la salud, lo que exige equipo de protección y sistemas de extracción, elevando los costos operativos y de limpieza.
Como proveedores de masterbatch y pigmento en polvo, es clave contar desde el inicio con información técnica completa del transformador para definir procesos eficientes. La falta de datos críticos en el desarrollo de color puede afectar la operación y rentabilidad, incluso si los efectos no son inmediatos.
1. Evaluación del color por el transformador
Es fundamental establecer con claridad el método de evaluación del color: espectrofotometría, colorimetría, inspección visual del pellet, de la ficha inyectada o del producto final fabricado. La falta de alineación entre proveedor y transformador puede generar discrepancias difíciles de resolver, con consecuencias como paros, mermas y retrasos. Definirlo desde el inicio garantiza procesos más eficientes y uniformidad entre lotes.
2. Pruebas físicas o químicas requeridas
El proveedor debe conocer desde el inicio qué pruebas de calidad exige el transformador (degradación, metales pesados, solidez a la luz, anclaje de tintas de impresión, etc.). Omitir esta información puede derivar en rechazos por incumplimiento, afectando la producción. Identificar estos requisitos permite anticipar necesidades específicas del masterbatch y evitar conflictos en validaciones internas.
3. Evaluación del producto fabricado por el transformador
Además de las pruebas internas del transformador, es clave conocer cómo evalúa su propio cliente final el producto fabricado. La falta de alineación en los criterios de calidad puede generar rechazos en cadena, afectando la operación de toda la línea. Tener claridad sobre estas pruebas permite asegurar que el desarrollo de color cumpla con los estándares en toda la cadena de suministro.
4. Fichas de control de color
Debe establecerse cuál ficha inyectada (gemela, muestra aprobada o primer lote) se usará como referencia, especificando el espesor y área de evaluación. Si el transformador califica el tono en una zona no representativa, podrían surgir rechazos por diferencias de interpretación. Acordar esta ficha y el espesor designado para los controles de calidad desde el inicio evita discrepancias y facilita aprobaciones consistentes.
5. Comportamiento de la muestra entregada con base al nuevo desarrollo de color
Es crucial evaluar la compatibilidad del masterbatch con la resina, su dispersión, tonalidad, presencia de grumos o carbonización, así como el porcentaje de aplicación. Si no se detectan desviaciones en esta etapa, los errores pueden replicarse en la producción, afectando la calidad desde el primer lote. Tener esta información asegura consistencia y eficiencia desde el arranque.
6. Evaluación del primer lote
El primer lote debe registrarse como punto de referencia colorístico, anotando cualquier efecto no deseado. Si no se documentan adecuadamente los parámetros usados, las variaciones entre lotes pueden generar retrabajos y rechazos. Registrar esta información permite mantener la uniformidad y reducir desperdicios.
7. Sistema de alimentación
Es importante especificar si el sistema es volumétrico, gravimétrico o manual. En especial, los sistemas volumétricos pueden generar inconsistencias por diferencias en la densidad granular, afectando la estabilidad del color. Conocer el tipo de alimentación permite ajustar la formulación y lograr una dosificación precisa que garantice uniformidad en el producto final.
Registrar correctamente estos requerimientos asegura que el resultado cumpla con las expectativas del cliente y previene desviaciones como:
- Rechazo de piezas por diferencias de tono
- Tiempos improductivos debido a paros de máquina
- Incremento en tiempo y frecuencia de limpieza de equipos
- Ajustes constantes en los parámetros del proceso
- Uso adicional de insumos no contemplados
- Incumplimiento en los programas de producción o ventas
- Necesidad de transporte adicional para recoger o reenviar productos no conformes
- Variaciones de color entre lotes
- Generación de inventarios obsoletos
Dar color a envases plásticos va más allá de la pigmentación; implica procesos claros, información precisa y colaboración constante. En Colorbatch, acompañamos cada etapa, desde la concepción hasta la validación en planta, para garantizar resultados rentables, eficientes y confiables.
Referencias:
• Expertos de Colorbatch
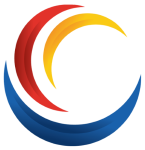